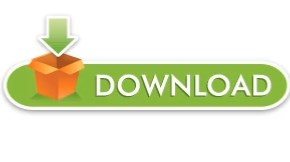
-1920w.png)
Uma metodologia eficiente e segura é proposta para prever a
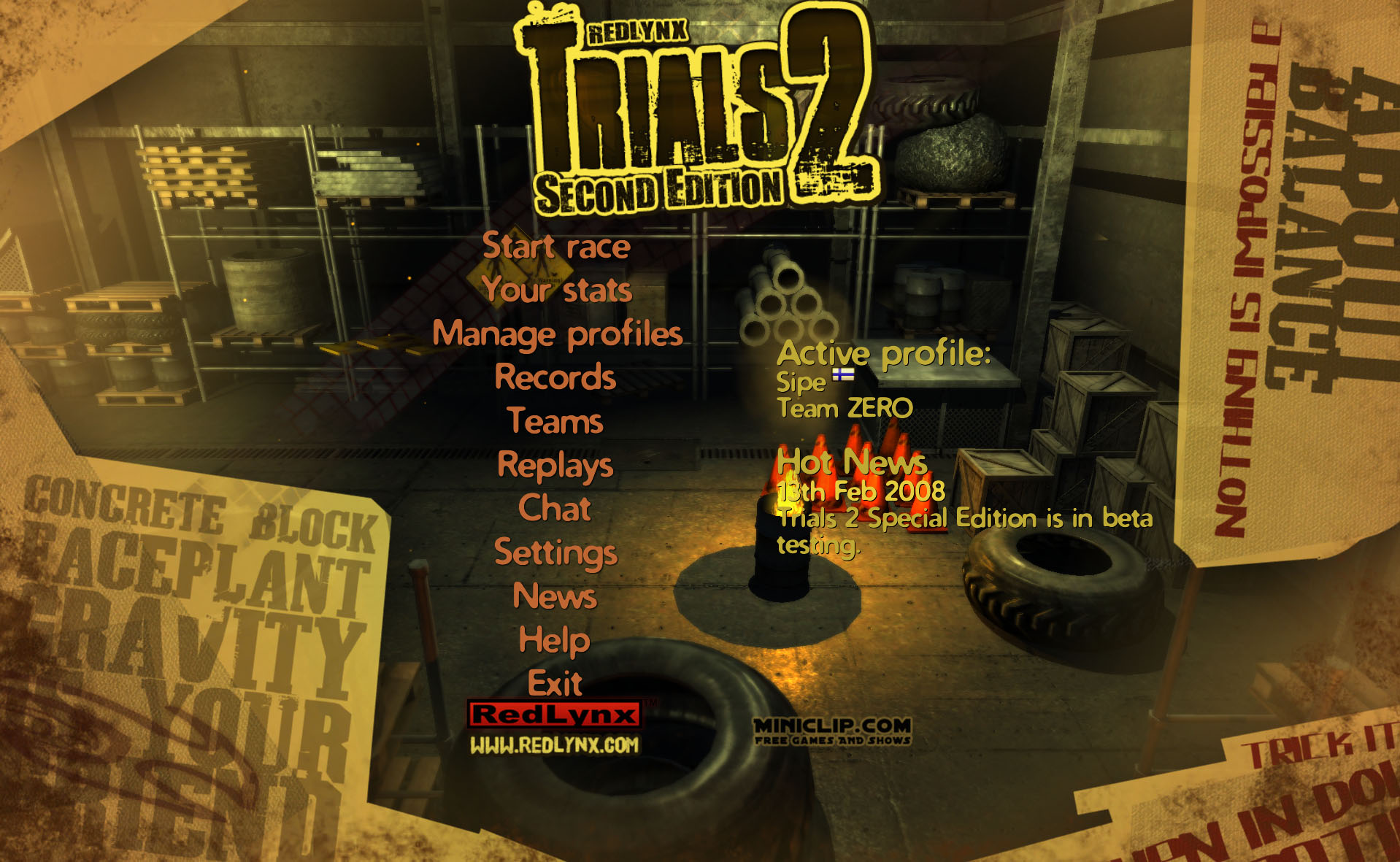
Also modelling long crack lengths has been perceived to be too computationally intensive and therefore studies focus on short crack lengths only.ĬONSELHO NACIONAL DE DESENVOLVIMENTO CIENTÍFICO E TECNOLÓGICO There are however still a number of issues regarding the modelling parameters such as mesh size, element type, number of loading increments and material hardening models that should be used and on whether crack closure represents the interaction effects sufficiently. Crack closure has been identified to be one of the main interaction factors, and finite element (FE) models have been developed to quantify it in terms of crack opening stresses. These factors which cause acceleration or deceleration of the crack growth are known as interaction effects. The estimation of da/dN under VA loading is complex due to effects of several factors such as plasticity, crack tip blunting, residual stresses, crack tip closure and crack tip branching which are associated with different levels of loading. The majority of work reported has focused on constant amplitude (CA) loading and some for variable amplitude (VA) loading. Several models have been proposed for estimating crack growth rate da/dN under various conditions. In these experiments, two different fatigue crack initiation directions are observed: horizontal and coplanar to the flaw.įatigue crack growth (FCG) is a major cause of failure in many engineering components and structures that are subjected to dynamic loading conditions.
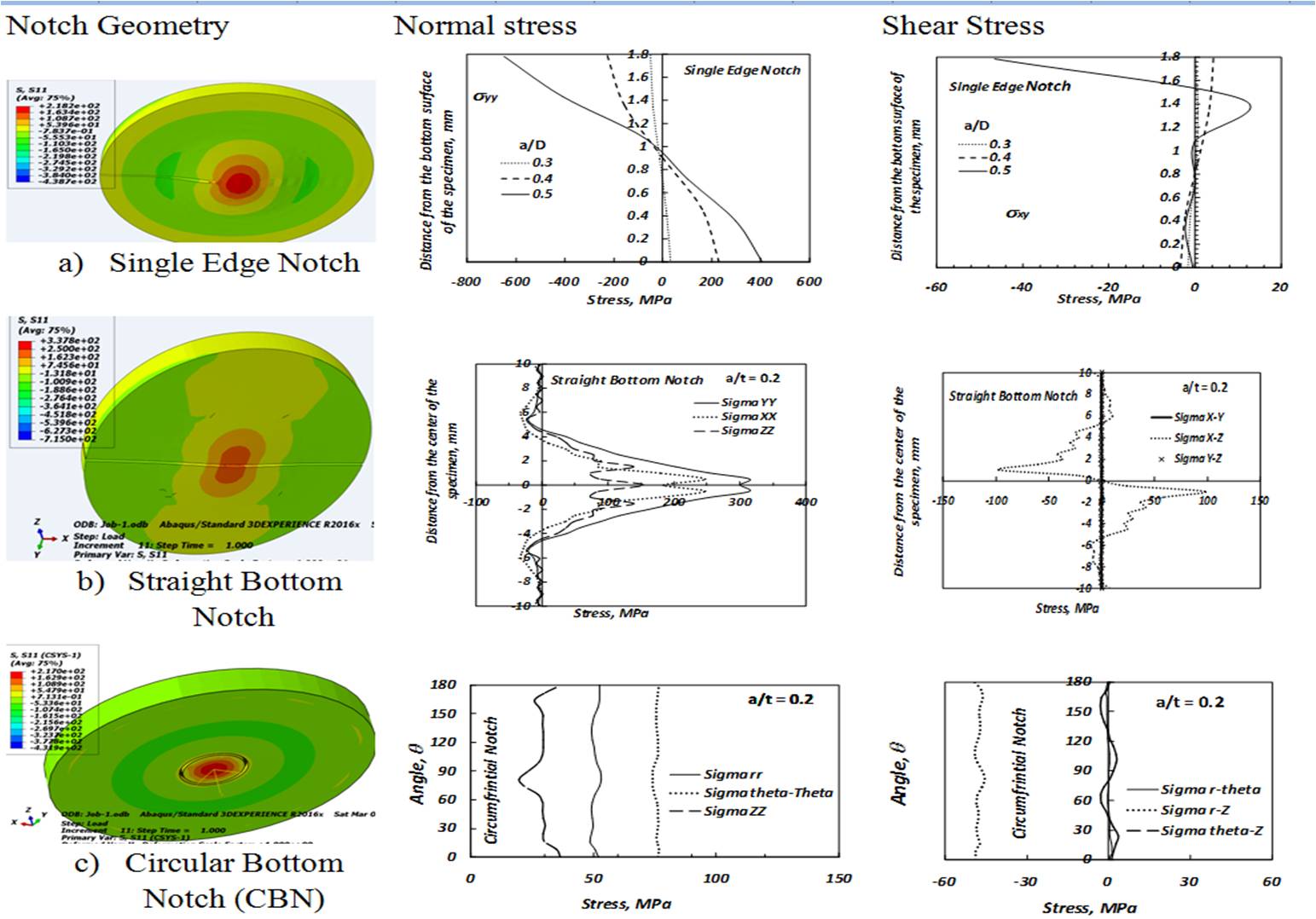
Fatigue cracks usually occur when 1) after coalescence, the specimens behave as if they had only one larger crack 2) specimens have been subjected to a particular number of cycles. Contrary to monotonic tests, cyclic tests produce fatigue cracks. For non-coplanar geometry specimens, coalescence occurs through combinations of internal shear cracks, internal wing cracks and tension cracks. For coplanar geometry specimens, coalescence occurs due to the internal shear cracks. Secondary cracks initiate at the tips of the flaws and propagate in the coplanar direction of the flaw or horizontal (quasi-coplanar) direction. Secondary cracks always appear after wing crack initiation and lead to final failure. Wing cracks, which are tension cracks, initiate at (or near) the tips of the flaws and propagate parallel to the compressive loading axis. Wing cracks and secondary cracks are observed in both monotonic and cyclic tests. The specimens have two pre-existing flaws which are arranged at different distances and angles. 181-184).Ī total of 170 tests (68 tests for monotonic loading, 102 tests for cyclic loading) have been performed to investigate crack initiation, propagation and coalescence. of Civil and Environmental Engineering, 2005. E.)-Massachusetts Institute of Technology, Dept.
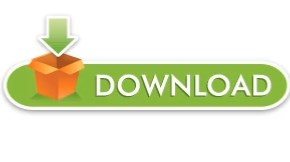